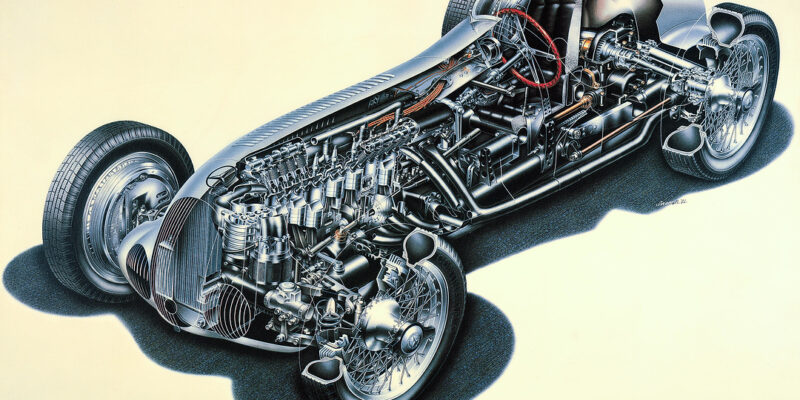
Karbonové šasi je jedním z nejdůležitějších a nejzajímavějších prvků vozu. Slouží jako základní konstrukce pro všechny ostatní komponenty a poskytuje ochrannou skořápku pro jezdce při vážných nehodách. V následujícím textu si přiblížíme základní pojmy a proces výroby karbonového šasi.
Doba přísavného efektu pravděpodobně připravila půdu pro další zásadní inovaci ve Formuli 1, a to zavedení karbonového šasi.
Když se konstruktéři soustředili na maximalizaci přísavného efektu, vedoucí designu McLarenu John Barnard se snažil najít způsob, jak co nejvíce zmenšit monokok, aby se zvětšil prostor pro venturiho tunely. Uvědomil si, že se zachováním potřebné torzní tuhosti by to s tradičním hliníkovým šasi nebylo možné. Významnou roli v tomto procesu sehrál Steve Nichols, nový člen týmu McLarenu, který měl zkušenosti s navrhováním kompozitních dílů pro raketové motory ve společnosti Hercules Aerospace. Díky spolupráci několika brilantních mozků vzniklo v roce 1981 na voze MP4/1 první šasi z karbonových vláken. Bylo lehčí, poskytovalo lepší torzní tuhost a co je nejdůležitější, zajišťovalo větší bezpečnost pro jezdce.
Kvalitní šasi je klíčové pro výkon vozu, protože musí poskytovat robustní a tuhou konstrukci, která dokáže zvládnout různé zatížení přenášená přes zavěšení, motor, převodovku a další komponenty. Nezapomínejme ani na palivovou nádrž, která je umístěna přímo za pilotem.
Pro dnešní vozy formule 1 je aerodynamický výkon hlavním faktorem, který ovlivňuje design šasi. Od začátku se šasi navrhuje s ohledem na aerodynamické požadavky, přičemž tvar karosérie je výrazně ovlivněn potřebami aerodynamických týmů. Obvykle se určí optimální tvar, který odpovídá koncepčnímu návrhu nového vozu, a konstrukční tým se snaží umístit jednotlivé komponenty do tohoto tvaru s co nejmenšími kompromisy.
Šasi obsahuje monokok, který je klíčovým prvkem propojujícím jezdce s vozem. Monokok přenáší „pocit“ odpružení, řízení, brzd a hnacího ústrojí na pilota. Tento pocit, známý v angličtině jako „driving by the seat of the pants“, přesně vystihuje, jak jezdec vnímá reakce vozu. Jeho celé tělo funguje jako jeden velký senzor, který umožňuje detekovat reakce vozu na různé síly a poskytuje zpětnou vazbu na všechny vstupy.
Jezdec sedí v anatomicky tvarované sedačce, která je přizpůsobena jeho tělu a umístěná co nejblíže k podlaze, aby mohl vnímat každou nerovnost na trati. Design a integrita šasi jsou nejen důležité pro pocit jezdce, ale i pro jeho bezpečnost, protože i malá poškození mohou mít vážné následky.
Šasi musí splňovat předpisy Mezinárodní automobilové federace (FIA), které stanovují minimální rozměry, umístění ochranných struktur pro případ převrácení a požadavky na pevnost měřenou nárazovými zkouškami. Inženýři FIA provádějí kontrolu referenčního šasi před začátkem sezóny a pouze šasi, které splní všechny požadavky, může být homologováno.
Podle předpisů nesmí homologované komponenty během sezóny podléhat konstrukčním úpravám nebo přestavbám. Vzhledem k velikosti a složitosti výroby šasi, která je náročná a časově náročná, je šasi prvním aspektem, kterému se konstrukční tým věnuje.
Tvar šasi a jeho návrh
Podvozek je doslova páteří celého vozu, a proto je výchozím bodem pro návrh vozu. Před jeho finalizací je nutné provést řadu analýz. Návrh nové konstrukce obvykle začíná v létě před nadcházející sezónou. Po několika měsících zdokonalování, analýz a strukturálních testů vzniká první referenční šasi, které je předloženo FIA k oficiálnímu testování v únoru následujícího roku. Šasi je obvykle poskytnuto přibližně čtyři až šest týdnů před prvním závodem.
V současnosti jsou všechny komponenty šasi vyráběny z kompozitů z uhlíkových vláken, které poskytují vysokou pevnost a směrovou tuhost při zachování nízké hmotnosti. V porovnání s alternativními konstrukcemi, jako jsou hliníkové rámy a plechové nebo hliníkovo-voštinové monokoky, mají kompozity z uhlíkových vláken výrazně lepší vlastnosti.
Moderní digitální technologie, jako CAD (počítačem řízený návrh) a CNC (počítačem řízené obrábění), mají velký vliv na výrobu. Tyto nástroje výrazně zrychlují a zefektivňují každý detail výrobního procesu, čímž zajišťují požadovanou kvalitu výrobku v oblasti rozměrů a tuhosti.
Díky těmto technologiím jsou všechny vyrobené díly prakticky totožné, což usnadňuje jejich výměnu bez ztráty efektivnosti. Jezdec téměř nikdy nedokáže rozlišit, který typ šasi je lepší, pokud je zachováno stejné nastavení vozu.
Cool F1 & LMP1 CAD models and CFD flows to manipulate online with @SimScale #perrinn pic.twitter.com/yqM3FFYbSc
— Craig Scarborough (@ScarbsTech) March 19, 2017
Výrobní proces od A po Z
Výrobní proces zahrnuje řadu důležitých kroků, které vám přiblížím ve zkrácené podobě. Většina velkých týmů ve formuli 1 má vlastní oddělení pro kompozity. Menší týmy se však z důvodu financí nebo nedostatku know-how obracejí na specializované společnosti, které pro ně vyrábějí uhlíkové komponenty.
Jak výroba probíhá?
- Analýza a kontrola: Celé šasi je důkladně analyzováno a kontrolováno, aby odpovídalo předpisům a poskytovalo požadovaný výkon. Používají se systémy CAD a metoda konečných prvků (FEM), která pomocí software předpovídá rozložení konstrukčních zatížení a vytváří barevně kódované trojrozměrné obrázky pro identifikaci slabých míst.
- Výroba vzorů: Po dokončení návrhu jsou pevné epoxidové vzory pro šasi vyřezány pomocí víceosých frézek, které přesně replikují požadované rozměry a obrysy. Epoxidové pryskyřice jsou vybrány, protože se roztahují podobnou rychlostí při vytvrzování ve vysokých teplotách. Přesnost vzorů je obvykle kolem 0,05 mm.
- Výroba forem: Vzory se používají k výrobě samičích forem v čistých místnostech, kde je pečlivě kontrolován tlak, vlhkost a teplota. Formy jsou vyrobeny z uhlíkových vláken a jejich výroba zahrnuje vakuové zpracování, vrstvení a tepelné vytvrzování. Počet a typ forem se liší podle týmu, někdy se vyrábějí horní a spodní formy, nebo se šasi vyrábí v několika sekcích.
- Úprava forem: Vnější povrchy hotových forem jsou opracovány, aby se odstranily ostré hrany a nedokonalosti. Formy se poté používají k výrobě šasi potřebných pro sezónu. Typický tým vyrábí čtyři až pět šasi ročně, včetně jednoho pro předsezónní nárazové testy.
- Vrstvení prepregu: Šasi je vyrobeno z vrstveného prepregu z uhlíkových vláken. Používá se několik typů laminátů a orientace vláken je kritická. V každém šasi je několik stovek vrstev uhlíkových vláken, které jsou různě strojově řezány pro přesnost a aplikovatelnost.
- Orientace vrstev: Počet a orientace vrstev se liší na různých místech šasi. Například kolem upevňovacích bodů, kde je vyžadována zvýšená pevnost. Orientace a umístění vrstev jsou určeny pomocí CAD softwaru a odborníci provádějí pokládku podle tištěných materiálů.
- Přidání voštiny: Po položení několika vrstev se do konstrukce vměstná voštinový materiál (obvykle hliník), který poskytuje dodatečnou tuhost bez výrazného zvýšení hmotnosti a přidává na nárazuvzdorných vlastnostech. Další vrstvy prepregu se položí na voštinu, čímž se vytvoří sendvičová konstrukce.
- Integrace komponentů: Během pokládky lze do konstrukce integrovat další součásti, jako kovové vložky a upevňovací kolíky, které slouží jako úchyty pro různé komponenty.
- Vytvrzování: Po položení vrstev se celá sestava vloží do vakuového sáčku a následně do autoklávu. Vysoké teploty a tlaky v autoklávu způsobí rovnoměrné roztečení pryskyřice a spojení vrstev do pevné struktury. Procesy v autoklávu jsou přísně tajné a liší se podle týmu.
- Sestavení šasi: Hotové části šasi se vyjmou z forem a spojí dohromady, aby vytvořily konečný monokok. Přepážky mohou být přidány pro držáky komponentů, a povrchy, které se mají spojit, musí být pečlivě očištěny.
- Finální úpravy: Provádí se finální opracování a ořezávání konstrukce, aby se vytvořily všechny požadované detaily.
- Kontrola kvality: V každé fázi výroby se dodržuje přísný kontrolní postup. Všechny díly a lepené sestavy jsou kontrolovány po vytvrzení, než jsou odeslány do další fáze výroby nebo konečného použití. Dílům se také provádí zpětná kontrola po vyčištění nebo opravě.
Ochranná skořápka jezdce
Ochranná skořápka šasi je klíčovým prvkem konstrukce. Poskytuje nejen extrémně pevný obal kolem řidiče, ale zahrnuje také struktury proti nárazu a převrácení. Titanová ochranná svatozář, která je samostatnou součástí, funguje jako další bezpečnostní prvek a poskytuje jezdci dodatečnou ochranu. Boky celé konstrukce jsou vybaveny ochrannými panely, které pomáhají snížit riziko vážných zranění způsobených nárazem jiného vozu nebo úlomkem.
Ochranná skořápka musí splňovat přísné předpisy a nárazové testy FIA. Od roku 2022 byly testy statického zatížení a nárazu výrazně upraveny, a nyní vyžadují, aby šasi absorbovalo o 48 % více energie než podle předpisů z roku 2021.
Ochrana proti bočnímu nárazu zahrnuje dva prvky:
- Neformovatelné konstrukce: Boky šasi jsou vybaveny neformovatelnými strukturami, které musí projít nárazovými testy. Na každé straně kokpitu musí být namontovány dvě takové konstrukce.
- Ochranné panely: Panely proti bočnímu nárazu jsou vyrobeny ze speciální tkaniny z prepregu z uhlíkových vláken a jsou nalepeny na boky šasi. Jejich umístění a tloušťka musí přesně odpovídat předpisům Mezinárodní automobilové federace.
Co se týče ochrany proti převrácení, před zavedením systému HALO v roce 2018 byla FIA stanovena povinnost začlenit do konstrukce dvě struktury proti převrácení. Jezdcova přilba a volant musely být umístěny ve specifikované vzdálenosti pod čarou mezi dvěma nejvyššími body těchto struktur. Po zavedení svatozáře se primární ochrannou strukturou stala ta umístěná za jezdcovou hlavou (blízko nasávání vzduchu pro motor), zatímco svatozář se stala sekundární ochrannou strukturou.
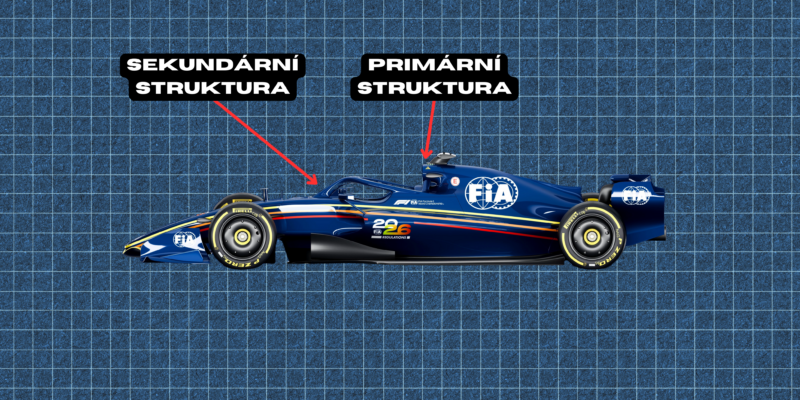
Kde se nachází palivová nádrž?
Palivová nádrž je umístěna v konstrukci šasi, konkrétně v zadní části kokpitu za sedačkou pilota. Aby vyhověla specifikacím FIA, musí být oddělena přepážkou.
Nádrž je vyrobena na zakázku specializovanými výrobci z kevlarového materiálu impregnovaného elastomerem. Tento materiál je lehký a extrémně pružný. Palivová nádrž je navržena tak, aby se deformovala při silném nárazu a zároveň je vysoce odolná proti protržení nebo proražení, čímž se minimalizuje riziko úniku paliva při nehodě.
Na nádrži je instalováno vnitřní tlumení hluku, vyrobené ze speciálních lehkých tkanin. Toto tlumení pomáhá snižovat šplouchání paliva při extrémních přetíženích. Palivová čerpadla uvnitř nádrže jsou pečlivě navržena tak, aby dokázala nasát i poslední kapky benzínu, což je důležité pro správné určení hmotnosti vozu.
My biggest highlights from the @Autosport_Show, on the @ATLFuelCells stand, Jaguar R4 F1 Fuel tank cutaway (AMAZING) pic.twitter.com/8RgJsMny
— Craig Scarborough (@ScarbsTech) January 12, 2013
Váha vozu a závaží
Když v roce 2014 začala éra hybridních pohonných jednotek, byl minimální hmotnostní limit zvýšen na 690 kg kvůli těžším a složitějším komponentům hnacího ústrojí. Pro rok 2015 byl limit opět navýšen, aby umožnil těžším pilotům snížit váhu vozu.
V následujících letech se hmotnostní limit postupně měnil, a pro rok 2021 činil 752 kg. Pro rok 2022 se limit zvýšil na 798 kg, přičemž důvodem byly nové předpisy, včetně větších a těžších pneumatik a nutnosti odolávat výrazně vyšším nárazovým silám.
Konstrukční tým se vždy snaží vytvořit vůz, který je pod minimální přípustnou hmotností, aby mohl být doplněn závažím. V minulosti bylo možné umísťovat závaží kdekoli v autě, pokud bylo pevně uchyceno. Obecně se závaží umisťovalo co nejníže, aby bylo těžiště co nejblíže k zemi. V posledních letech však pravidla určují, že závaží musí být umístěno v oblasti kokpitu a musí být upevněno nástroji. Každé závaží je zapečetěné FIA a musí být označeno, takže během závodu nelze závaží upravovat.
Pravidla také stanovují, že hmotnost jezdce včetně jeho vybavení (oblečení, přilba, HANS a sedačka) musí být připočtena k celkové hmotnosti vozu a nesmí být nižší než 80 kg.
Na každý dodatečný kilogram hmotnosti vozu se jeho čas na kolo zhorší přibližně o 0,03 sekundy. Pokud je vůz navržen s nižší hmotností než stanovený limit, musí tým dosáhnout požadované minimální hmotnosti pomocí závaží. Vzhledem k tomu, že většina vozů formule 1 je velmi citlivá na změny v hmotnosti, mohou být znatelné rozdíly již při přidání 500 gramů.
Přední nárazová struktura
Přestože není přední nárazová konstrukce součástí samotného šasi, musí být pevně připevněna k jeho přední části, aby efektivně absorbovala síly při nárazu. Na rozdíl od nárazových zón u běžných silničních vozů, které pohlcují energii deformací, jsou nárazové struktury z uhlíkových vláken ve vozech F1 navrženy tak, aby energii absorbovaly tím, že se rozpadnou. To je důvod, proč je často vidět na trati při nehodě velké množství úlomků.
V roce 2022 byla přední struktura výrazně posílena a nyní musí absorbovat o více než 50 % více nárazové energie než v předchozích letech. Důvodem je také smrtelná nehoda Anthoina Huberta ve formuli 2 ve Spa, která se stala v roce 2019.
Zadní nárazová struktura
Princip zadní nárazové struktury je téměř stejný jako u přední. Zadní nárazová konstrukce je připevněna k zadní části převodové skříně a kromě toho, že je navržena k absorbování nárazů, slouží také jako montážní bod pro zadní světlo a úchyt pro zvedák. V minulých sezónách některé týmy používaly zadní nárazovou strukturu k umístění prvků zadního křídla.
Od roku 2022 předpisy vyžadují, aby byla zadní nárazová konstrukce spojena se skříní převodovky pomocí speciálního uchycení, které zabrání vylétnutí nárazové konstrukce ze skříně převodovky.
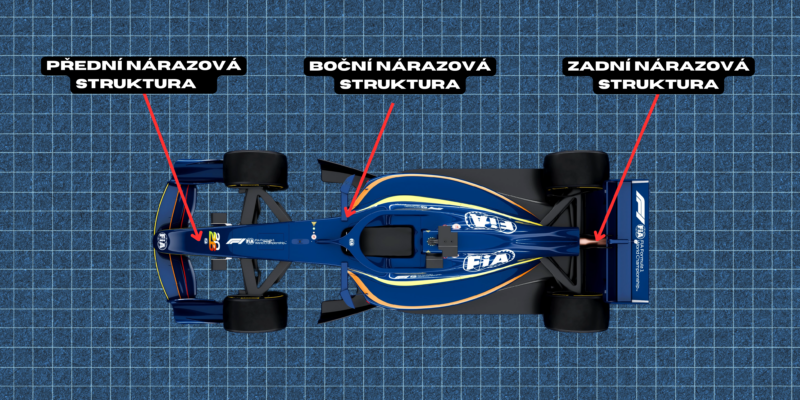
Tuhost šasi
Jak už bylo zmíněno, šasi musí být dostatečně pevné, aby odolalo silám, kterým je vystaveno. Torzní tuhost podvozku lze otestovat, a většina týmů to dělá s každým nově vyrobeným šasi. Tento test poskytuje referenční bod, který lze použít k porovnání podobných měření během sezóny, aby se zjistilo, jak si konkrétní specifikace vede a zda nedošlo k nějakému významnému poškození.
Obecně platí, že největšímu zatížení jsou vystaveny dvě oblasti: upevňovací body předního zavěšení a upevňovací body motoru. Je důležité si uvědomit, že zatížení z předního zavěšení se přenáší přímo do konstrukce přes převodovku a motor. Proto by všechna šasi měla mít podobnou tuhost, což by mělo být zajištěno výrobním procesem.
Pokud během sezóny dojde k poškození šasi, existuje několik možností, jak opravu usnadnit – od vstřikování pryskyřice až po nalepení úplně nové sekce. Výběr metody závisí na typu a závažnosti poškození.
Skvělým příkladem v této oblasti jsou Kimi Räikkönen a Ayrton Senna. Oba byli přesvědčeni, že i drobné trhliny nebo poškození šasi mohou výrazně ovlivnit výkon vozu. Jejich schopnost vnímat detaily je často vedla k tomu, že od svých týmů vyžadovali důkladné prohlídky a někdy i výměnu šasi, pokud cítili, že s vozem není něco v pořádku. Tato preciznost a pozornost k detailům nejenže přispěla k jejich úspěchům ve formuli 1, ale také ukázala, jak zásadní je pro jezdce dokonalé propojení s vozem.
V příštím díle si přiblížíme, jakým způsobem funguje aerodynamika.